Introduction
Ignoring even one safety protocol can cost your company more than fines—it can put lives and reputations on the line. 😮 Many organizations assume that following the bare minimum is enough, but fast-changing standards and increased scrutiny demand a higher level of vigilance. This guide gives you practical clarity on what “workplace safety compliance” truly means, how to put airtight systems in place, and where to start if you want compliance to drive—not hinder—your business.
What you need to grasp right now:
- The real impact of compliance goes far beyond legal protection—it shapes your culture and bottom line
- Effective safety programs hinge on training, clear procedures, and relentless follow-through
- You’ll walk away able to spot hidden compliance risks and know how to build improvements into your daily operations
What Is Workplace Safety Compliance?
Think of workplace safety compliance as the set of rules and actions businesses must follow to keep their employees safe and healthy on the job. It’s about actively identifying potential dangers—like slippery floors, faulty equipment, or exposure to harmful substances—and putting measures in place to prevent accidents or injuries. This isn’t a one-time check; it’s a continuous effort to meet legal requirements set by government agencies and industry bodies.
The core purpose is straightforward: protect people. But it goes deeper than that. Strong compliance creates a workplace where employees feel secure and valued. It also shields the business from hefty fines, lawsuits, and damage to its public image. As work environments change, new technologies emerge, and different hazards appear, safety compliance must adapt too, making it a living, breathing part of how a responsible business operates.
“Safety compliance is the continuing process of meeting regulations that ensure the occupational health and safety of employees, reducing hazards and risks within a workplace.” -Fluix
Core Principles: Laws, Regulations, and Standards
At the heart of safety compliance is a framework of rules. In the United States, the Occupational Safety and Health Administration (OSHA) sets the primary federal standards. Beyond OSHA, businesses might also need to follow state-specific laws, local ordinances, and standards developed by specific industries (like construction or healthcare) which often have unique risks. These rules cover everything from machine guarding and chemical handling to emergency exits and noise levels.
It helps to understand the hierarchy: Laws (like the OSH Act) create the legal obligation; Regulations (like specific OSHA rules) detail *what* must be done; Standards (often from industry groups or consensus bodies like ANSI) provide accepted methods for *how* to meet those regulations. Companies also develop their own internal safety policies, which should meet or exceed legal minimums. Staying current with all these layers is vital, as rules can change based on new research, technology, or unfortunate incidents. 📜
“Safety compliance standards are a comprehensive set of rules, regulations, and guidelines that are designed to ensure the safety and health of employees.” -SiteDocs
Employer Responsibilities: What Must Be Done?
Employers carry the primary legal weight for ensuring a safe workplace. This isn’t just about good intentions; it involves concrete actions. A fundamental duty is to identify and assess potential hazards specific to their operations. This means actively looking for dangers, from obvious physical risks to less visible ones like ergonomic strains or chemical exposures, and taking steps to eliminate or control them using tools like asset tracking software.
Other key obligations include providing necessary safety training so employees know how to do their jobs safely and understand the risks involved. Employers must supply appropriate personal protective equipment (PPE) like gloves, goggles, or respirators at no cost to employees. Maintaining accurate records of work-related injuries, illnesses, safety training sessions, and hazard assessments is also mandatory. Fundamentally, the law requires employers to provide a work environment free from known, serious dangers. ✅
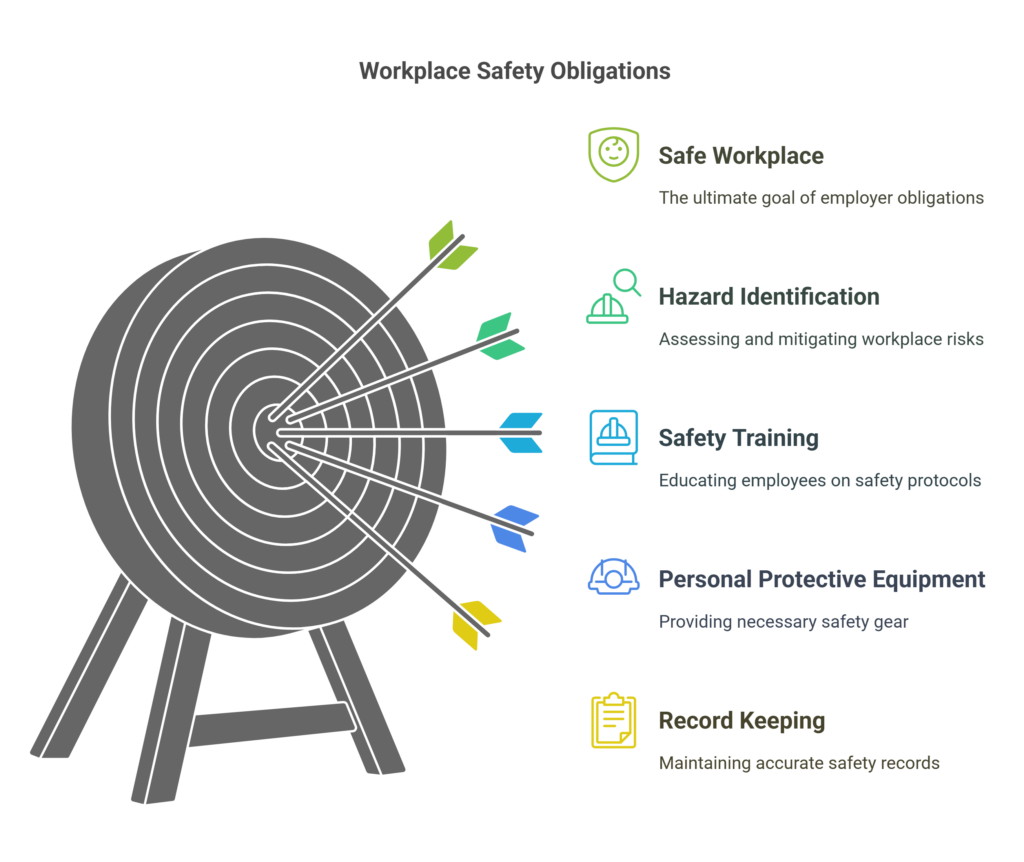
“Provide a workplace free from serious recognized hazards and comply with standards, rules and regulations issued under the OSH Act.” -OSHA
Employee Rights and Participation in Safety Compliance
While employers hold the main responsibility, employees have legally protected rights concerning workplace safety. They have the right to receive information and training about job hazards, prevention methods, and the safety standards that apply to their workplace, presented in a language they understand. Employees can also request copies of workplace injury logs, results from tests done to find hazards, and relevant safety standards.
Critically, employees have the right to report safety concerns or injuries to their employer or directly to OSHA without fear of retaliation or discrimination. Encouraging employees to actively participate is essential for effective compliance. When workers feel comfortable pointing out potential risks, suggesting improvements, and joining safety committees or discussions, the entire safety program becomes stronger and more practical. Their frontline perspective is invaluable.
“Whether they know it or not, employees are entitled—by federal law—to a safe workplace, free of recognized health and safety hazards.” -DuraMark Technologies
Common Compliance Requirements Across Industries
While certain rules are highly specific to industries like construction or healthcare, many safety compliance requirements are common across the board. Conducting regular risk assessments to identify potential job hazards is almost universal. Posting mandatory safety information, such as the OSHA Job Safety and Health poster, in a visible location is another common requirement. Providing safety training tailored to job roles and potential exposures is also fundamental.
Establishing clear procedures for reporting incidents, injuries, and near-misses is critical everywhere. Many workplaces also need protocols for emergency response, fire prevention, and the proper use and maintenance of PPE. Although these elements form a common baseline, businesses must always layer on any industry-specific regulations (e.g., lockout/tagout for manufacturing, bloodborne pathogen standards for healthcare) to ensure full compliance.
“Health and safety rules vary from country to country, but they all aim to protect people at work.” -YouFactors
Procedures, Training, and Internal Communication
Written safety procedures are the backbone of a compliant workplace. These aren’t just dusty manuals; they should be clear, step-by-step guides on how to perform tasks safely, handle equipment correctly, respond to emergencies, and use protective gear. Think of them as the operational playbook for safety. Having these documented makes expectations clear and provides a consistent reference point for everyone. 📝
Training brings these procedures to life. It ensures employees not only know *what* the rules are but *why* they exist and *how* to follow them effectively. Training needs to be ongoing – not just for new hires, but regular refreshers and updates whenever procedures change or new hazards emerge. Open communication channels are equally important. Encouraging feedback, holding safety meetings, and making safety information easily accessible keeps compliance top-of-mind and allows for continuous improvement based on real-world experiences.
“Procedures are step-by-step instructions that describe how to perform specific tasks safely…Training provides employees with the knowledge and skills they need to perform their jobs safely.” -SafetyMint
Building a Safety Culture: Leadership and Buy-in
Compliance checklists and procedures are necessary, but they only work effectively within a strong safety culture. This starts at the top. When leaders actively demonstrate their commitment to safety—by following rules themselves, allocating resources for safety initiatives, and prioritizing safety over shortcuts—it sends a powerful message throughout the organization. Lip service isn’t enough; leadership actions set the tone.
Genuine employee buy-in is the other crucial ingredient. If workers see safety compliance as just another bureaucratic hurdle or something management imposes without understanding their jobs, they’re less likely to be engaged. Fostering a culture where employees feel empowered to speak up, participate in safety decisions, and look out for one another transforms compliance from a mandate into a shared value. This collective ownership makes safety practices stick. 👍
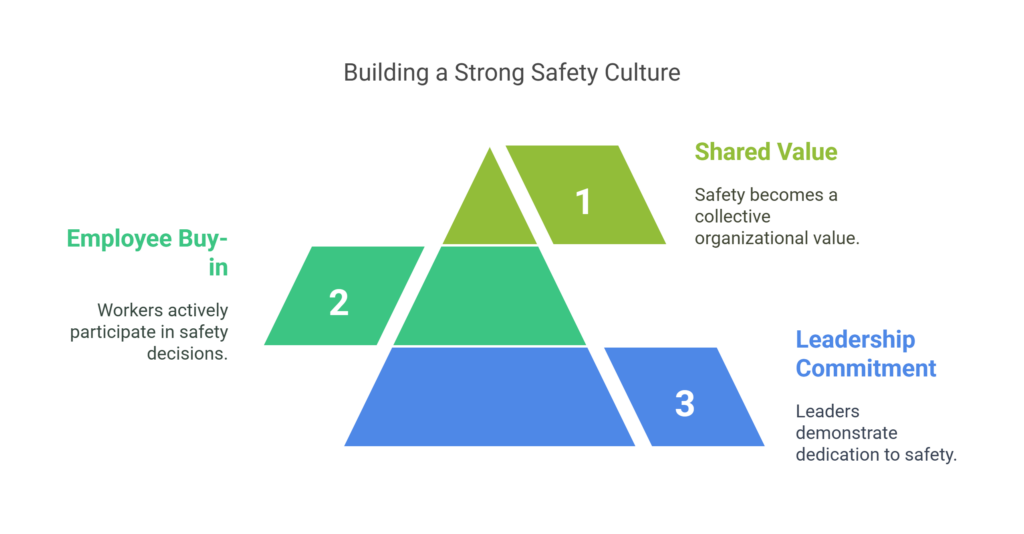
“The success of a safety compliance program depends on the commitment and involvement of management. Management plays a crucial role in creating a culture of safety within the organization.” -SafetyMint
Monitoring, Auditing, and Continuous Improvement
Achieving compliance isn’t a destination; it’s a journey that requires constant attention. Regular monitoring and auditing are essential to verify that safety procedures are actually being followed and remain effective. This involves conducting internal inspections, reviewing safety records, observing work practices, and checking that equipment is properly maintained and PPE is used correctly. Think of it as a health check for your safety program.
These audits shouldn’t just be about finding faults; they’re opportunities for learning and improvement. Analyzing incident reports, near-misses, and audit findings helps identify weaknesses or emerging risks. This information should feed back into refining procedures, updating training, and making necessary changes to the work environment. A commitment to continuous improvement ensures the safety program evolves alongside the business and stays relevant to current risks. 🧐
Consequences of Non-Compliance
Ignoring or neglecting workplace safety compliance can have severe repercussions that ripple through an entire organization. The most obvious are the legal and financial penalties. OSHA and other regulatory bodies can issue substantial fines for violations, which can escalate significantly for repeat or willful offenses. Beyond fines, businesses may face lawsuits from injured employees or their families, leading to costly legal battles and settlements. 💸
The damage often extends far beyond monetary costs. A serious incident or a pattern of non-compliance can irrevocably harm a company’s reputation, eroding trust among employees, customers, and the public. This can make it harder to attract and retain talent and may even impact business partnerships. Most importantly, non-compliance puts people at risk, potentially leading to life-altering injuries or fatalities—the ultimate, tragic cost that no business can afford, as highlighted in our case studies showing the benefits of robust systems.
Technology’s Role in Modern Compliance Management
Keeping up with safety compliance can feel overwhelming, especially with complex regulations and extensive documentation needs. Thankfully, technology offers powerful tools to streamline these processes. Specialized software platforms can centralize safety data, track training records, manage inspection schedules, and simplify incident reporting. Automation can handle reminders for recurring tasks like audits or certification renewals.
Digital tools make documentation much easier to manage, store, and access compared to paper-based systems. Mobile apps allow workers to report hazards or complete checklists directly from the field. Dashboards can provide real-time insights into safety performance, helping managers spot trends and address issues proactively. Using technology helps ensure accuracy, improves efficiency, and makes demonstrating compliance to regulators much simpler. 💻
Workplace Safety Compliance in High-Risk Industries
While safety is important everywhere, compliance takes on heightened significance in high-risk industries like construction, manufacturing, oil and gas, and healthcare. These sectors face unique and often severe hazards, from heavy machinery and fall risks on construction sites to chemical exposures and complex processes in manufacturing, or infectious diseases and patient handling in healthcare. Consequently, regulations are often more stringent and numerous.
Factors like high workloads, tight deadlines, and constantly changing environments can increase pressure and risk in these fields. Effective compliance requires meticulous risk assessment tailored to specific tasks and sites, robust training programs addressing specialized hazards, and rigorous adherence to protocols like lockout/tagout or infection control. Understanding and managing the interplay between work demands and safety protocols is absolutely critical.
“Safety compliance is one of two components of the phrase ‘safety behavior,’ which is more widely used in safety performance system research.” -National Institutes of Health (NIH)
How Nektar.io Makes Compliance Simpler and More Effective
Navigating the complexities of workplace safety compliance can be challenging, but platforms like Nektar.io are designed to help. Nektar.io provides tools specifically built to support organizations in managing their safety obligations effectively. It helps centralize crucial safety documentation, making it easy to store, update, and access policies, procedures, and training records when needed.
By streamlining tasks like scheduling safety audits, tracking corrective actions, and managing employee training completion, Nektar.io helps ensure nothing falls through the cracks. Its features align directly with the core compliance activities discussed earlier—from facilitating hazard reporting and incident management to supporting communication and demonstrating due diligence. For businesses looking to strengthen their safety programs and simplify compliance management, Nektar.io offers a practical, modern approach. ✨
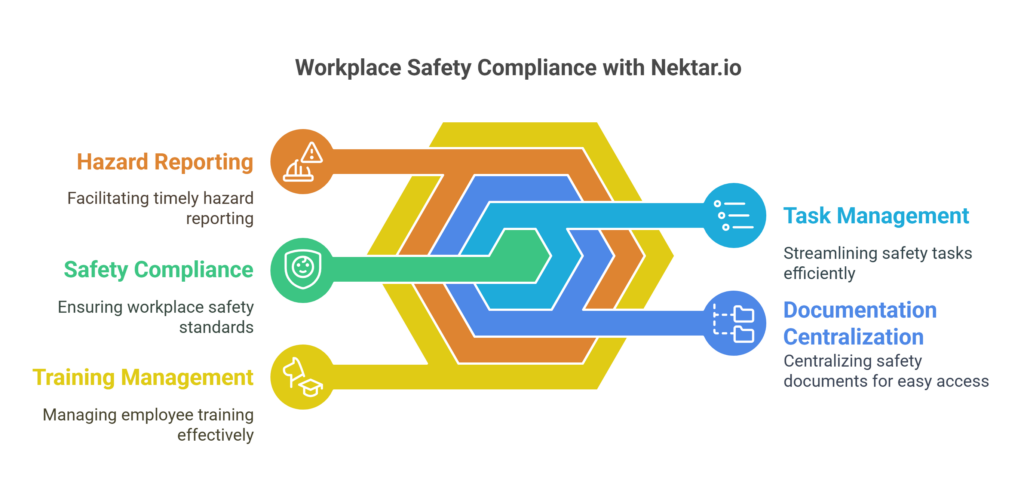
Frequently Asked Questions about Workplace Safety Compliance
- What is workplace safety compliance and why is it required?Workplace safety compliance involves following legally mandated rules (like OSHA standards) and best practices designed to protect employees from job-related hazards. It’s required by law to prevent injuries and illnesses, ensuring employers provide a safe working environment, and failure to comply can lead to significant penalties.
- What are the most common workplace safety compliance requirements?Common requirements include providing job-specific safety training, displaying mandatory safety posters, having clear procedures for reporting incidents, ensuring proper use of Personal Protective Equipment (PPE), conducting regular hazard assessments and safety audits, and maintaining accurate records.
- Who enforces workplace safety regulations?In the U.S., the primary federal enforcement agency is OSHA. Many states also have their own OSHA-approved state plans that enforce safety regulations, which must be at least as effective as federal OSHA. Certain industry-specific organizations or regulatory bodies may also have oversight roles.
- How often should safety training and audits be conducted?Frequency depends on regulations and risks. Initial training is required for new hires or new job tasks. Refresher training is often needed annually or when standards change. Audits should be conducted regularly (e.g., quarterly or annually, depending on complexity) and after incidents or significant operational changes.
- What are the penalties for non-compliance?Penalties can include significant monetary fines from regulatory agencies like OSHA, potential civil lawsuits from affected employees, criminal charges in cases of willful negligence leading to death, increased insurance premiums, operational shutdowns, and substantial damage to the company’s reputation. Check our FAQ for more details.
Conclusion
Workplace safety compliance is not a box to check, but a dynamic commitment that shapes every aspect of your organization—from morale to the bottom line. With shifting regulations and rising expectations, proactive compliance protects your people and your reputation. 🛡️
Nektar.io streamlines compliance management with tools built for real-world requirements, keeping your business current and your teams safe. Don’t leave safety to chance—explore how Nektar.io can strengthen your compliance strategy now.
Key Takeaways:
- Workplace safety compliance is an ongoing, legally enforced responsibility that protects employees and employers
- Effective compliance relies on clear procedures, regular training, and leadership engagement
- Modern tools like Nektar.io simplify compliance processes, supporting documentation, audits, and workforce participation
- Non-compliance can lead to severe legal, financial, and reputational damage—make compliance a core part of your operation