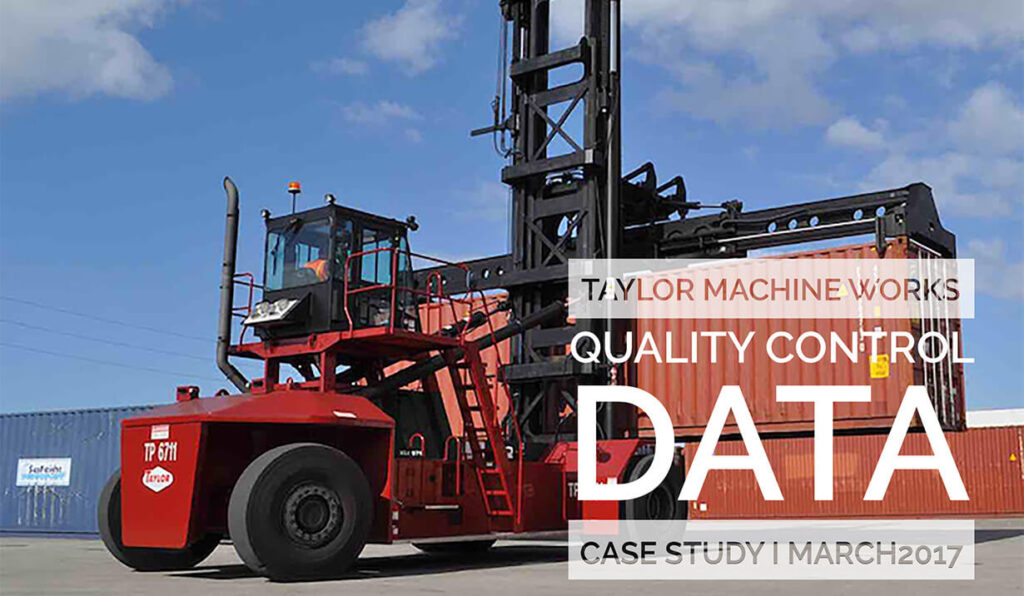
Taylor Machine Works has been in business for 87 years. Their intense focus on the quality of the customized forklift trucks that they manufacture has led them on a journey of longevity that matches that of their products and has allowed them to become a world-wide organization with state-of-the-art engineering and manufacturing resources.
The Challenge
Much has changed over the last 87 years, however, and even though the company continues to enjoy long term success, Taylor Machine Works needed a tool that would allow them to track data collected from specific assets in the Quality Control Department, in order to ensure that their high standards could be upheld in an industry that is constantly evolving.
In spring of 2013, Kale Moody was moved into the position of Quality Control Manager for Taylor, and almost immediately sought a solution that would help him and his team drive quality to a new level by providing them with a way to track deficiencies accurately and easily by identifying problem areas and tracking improvements.
The Challenge with Paper Data Collection
Taylor builds customized, industrial forklift trucks and each of these goes through a series of checks to ensure that their high standards are upheld and that the customer will be getting what they’re supposed to, and that the products are consistent with the highest quality, safe, and functional.
Data collected during these quality checks throughout the manufacturing process had always been gathered using paper, which presented challenges for Moody and the quality control team. Having the data collected on paper allowed the team to record the results of the checks and inspections but left them with a disjointed system of information that could not be used practically beyond simply a recording tool. Important information was being gathered through these checks, but they were unable to make good use of it.
With paper, it was difficult to draw big-picture conclusions based on the collected data, because it was practically impossible to compile it in a way that would be meaningful to the team and that would allow decision-makers to determine the proper courses of action.
Adopting an Electronic Data Collection System
Moody began searching for a paperless data collection system that would allow his crew to collect necessary data using mobile devices and associate the information directly to an asset. The intent was to have a system that would allow the company to ensure excellent manufacturer quality control by being able to track data historically in order to identify problem areas, address them, and track the improvements.
Kale sifted through many potential products and tested two or three, but all that was offered were products that were one-size-fits-all and not at all customizable to Taylor’s needs.
After a while, Moody was introduced to Nektar’s mobile data and asset management platform. Not only was the tool a completely blank page that the Nektar team would build to fit Taylor’s needs, but Nektar also used industrial-strength adhesive QR tags to uniquely identify individual assets and then record, store, retrieve and utilize information pertaining to all checks and inspections for each asset.
The QR tags acted as a license plate to the asset and a conduit to and from the database; whatever checks or electronic inspections were done would be recorded into the database and tied directly to a specific asset.
Realizing the Potential of Mobile Data Collection
Moving from a paper-based system to electronic was necessary and took effort, organization, and strong leadership; however, Moody reports that pushback was minimal to non-existent.
“Most people, once they realized the potential of it, that was not an issue. It benefits the people working because it’s less hassle and less paperwork.” Kale Moody
The mobile data collection tool allowed the quality control team to trace, track and watch data while being able to attach it to a specific asset. The same checks and quality control inspections were still being completed during the manufacturing process, but rather than data being collected on paper, workers would perform their regular work, record the necessary information about a specific asset using their smartphones. They would then scan the QR tag attached to the piece of equipment being checked, and the information would be stored forever in the database and directly associated with that asset. The data could then be retrieved from the database using a smartphone by scanning the tag, or on the desktop by searching, sorting, querying or filtering by any of the assets’ unique attributes.
Nektar Reporting
Perhaps most useful for Taylor is the ability to view necessary information and trends with the Nektar reporting tool, allowing for the most efficient use of the data. The Nektar reporting function is used to isolate only the information that users wish to see in an easy-to-read electronic format. For example, for workers on the floor, each individual can pull up a report that shows them only the things that they need to fix, providing Taylor with the ability to filter information depending on who needs to use it.
This provided Taylor with the ability to identify any problem areas, such as the number of deficiencies or a high reject percentage in certain areas, address the issues, monitor improvements, and continuously view progress in order to get better.
The Benefits of Mobile Data Tracking for Quality Control
As far as Kale Moody is concerned, the value of Nektar’s platform is just beginning to be tapped. The many benefits that have been realized so far include:
- The improved quality control system
- Robust electronic record keeping
- Reduction in manufacturer deficiencies
- Reduction in reject percentages
- Having an entire history of all asset checks and inspections at Taylor’s disposal
- Increase in efficiency of quality control processes
- Elimination of paperwork
- Reduction in the amount of physical space needed to store paper documents of checks and inspections
- Elimination of lost paper and important information, reducing the time needed to redo checks and inspections
- The ability to make changes to checks and inspections on the fly and all changes are reflected immediately across all users’ devices
- Possibility of further integration in the company with the product, due to its versatility
- Using historical data for future learning for people that may not yet be a part of the company
With almost a year of useful, accessible data at their fingertips, Taylor Machine Works is beginning to use the information that has been collected over the months to identify trends from the checks and inspections. The most valuable part of the system according to Moody is that for the first time, using the data, the company is able to identify the problem areas, focus on the perfection of those areas, and track and monitor the improvements, while being able to show the occurring progression of the improvements.
The Results
The versatility of the Nektar platform has led Taylor Machine Works to explore the possibility of using it in other areas of the business beyond quality control.
“It has opened the door for a lot of other opportunities! Over time, I feel that we would use it in much more of a production and management area. Instead of going back and forth running to the PC and looking for information, all that information will be there handy, no matter where you are in the plant and Nektar will be a big part of that.” Kale Moody
It is the dedication to quality, safety, and customer satisfaction that has been the reason that Taylor Machine Works has been around so long and is an industry leader in the production of forklift trucks. The ability to collect data electronically and use it to reduce manufacturer deficiencies and track reject percentages has made Nektar a valuable asset to the company. With the progressive nature of the Quality Control Division under Moody’s leadership, and armed with a powerful tool like Nektar, the team will no doubt continue to get better and will provide their customers with high quality, safe, functional equipment for another 87 years.